- Home
- Business Optimization
- Solutions
- Engineering Solutions
- Direct Fastening System
- Fastening on Steel
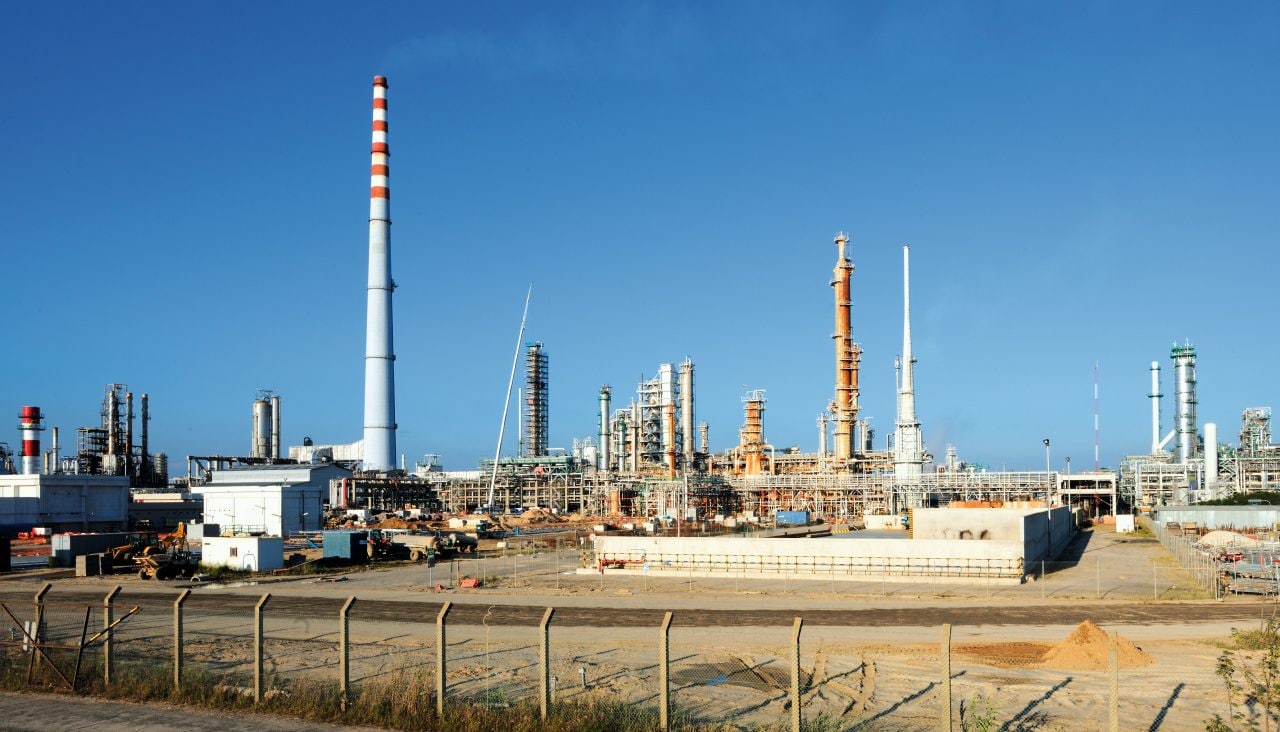
Fastening on steel in corrosive environments
Hilti provides a range of faster, more reliable and efficient solutions for fastening to steel
Ideal for corrosive environments, such as the energy and industry sector.
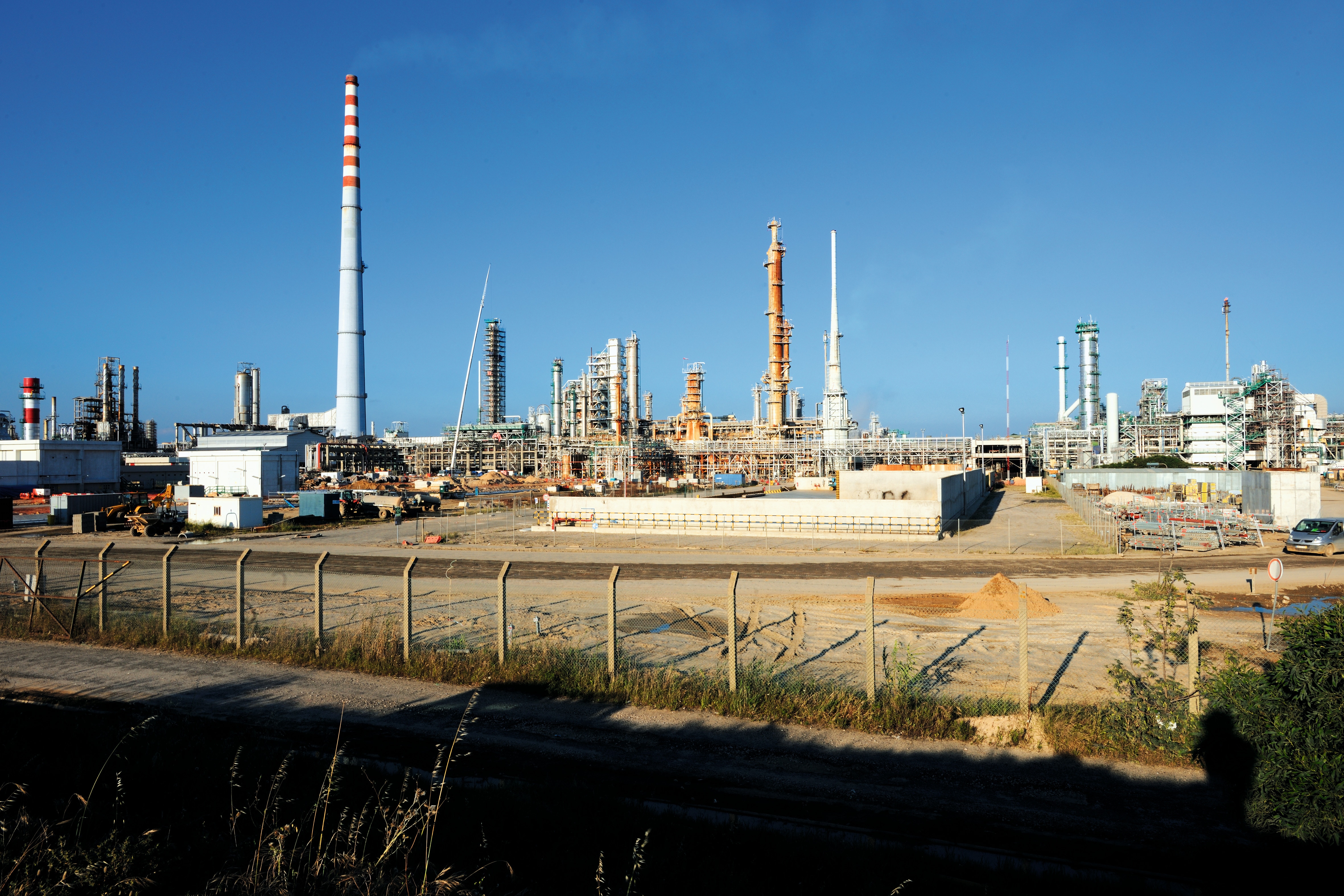
When you think that your medium-to-large project may need as many as 100,000 fastenings to attach components to structural steel, a faster method for corrosion-resistant fastenings would seem long overdue.
With such volumes, design engineers and contractors working in corrosive environments – like oil & gas, petrochemical, and power & utilities projects – would welcome faster and more efficient ways of fastening components to structural steel. As an additional challenge, the components – such as grating, strut, conduit, cable trays, pipes, electrical boxes, supports for instrumentation panels, etc. – and the fasteners are often exposed to harsh weather, pollution and coastal environments, therefore requiring corrosion protection.
The structural steel may be hot-dip galvanized or coated with paint to help provide adequate corrosion protection depending on the specific environment. However, when fastening components, design engineers and contractors must ensure the corrosion protection of the structural steel is not compromised. The traditional fastening methods used under these conditions include welding, through-bolting and clamping. In this editorial we will compare these with the Hilti methods for fastening on steel and show how Hilti can help save you both time and money.
Hilti Direct Fastening VS. Traditional Methods
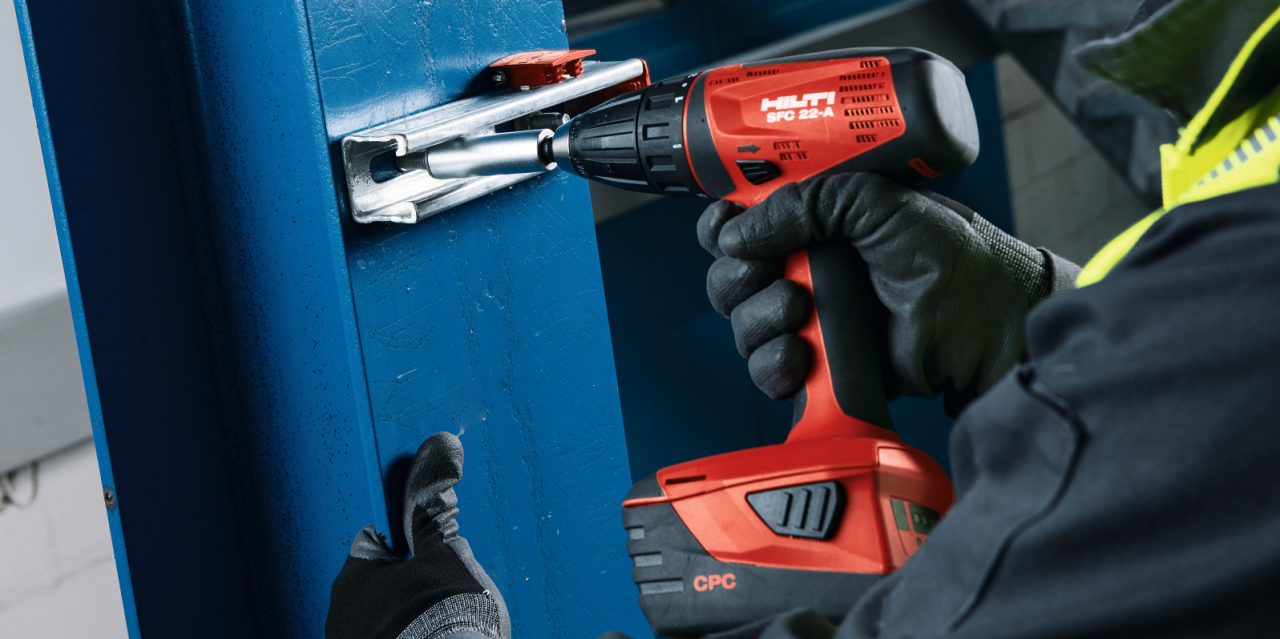
Hilti Direct Fastening
- Extremely fast process
- No external power source needed
- Weather independent
- No rework of coated steel
- Vibration resistant
- Requires access from only one side
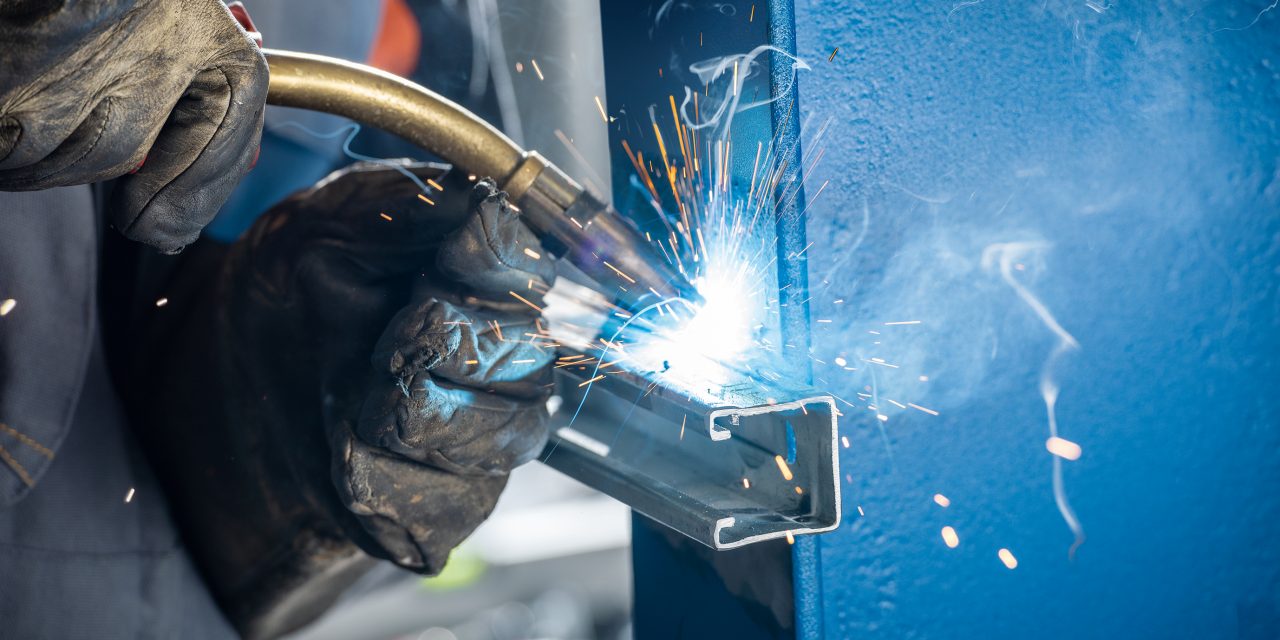
Traditional Method ─ Welding
- Certified welders needed ─ higher labor costs
- Preparation & rework of coated steel ─ longer fastening process
- External power source needed
- Dependent on weather conditions
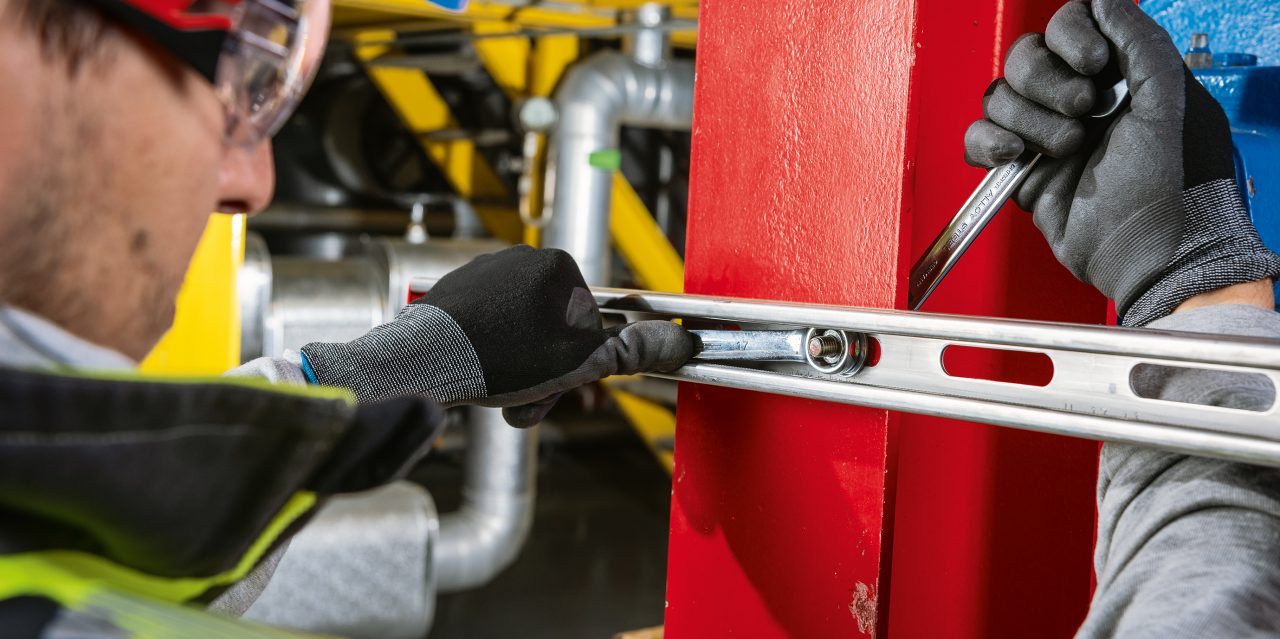
Traditional Method ─ Bolting
- Through-penetration of steel flange ─ affects steel load capacity
- Access from 2 sides needed
- Rework of coated steel required ─ longer fastening process
- Long and tedious process, especially with thick steel flanges ─ high waste of drill bits
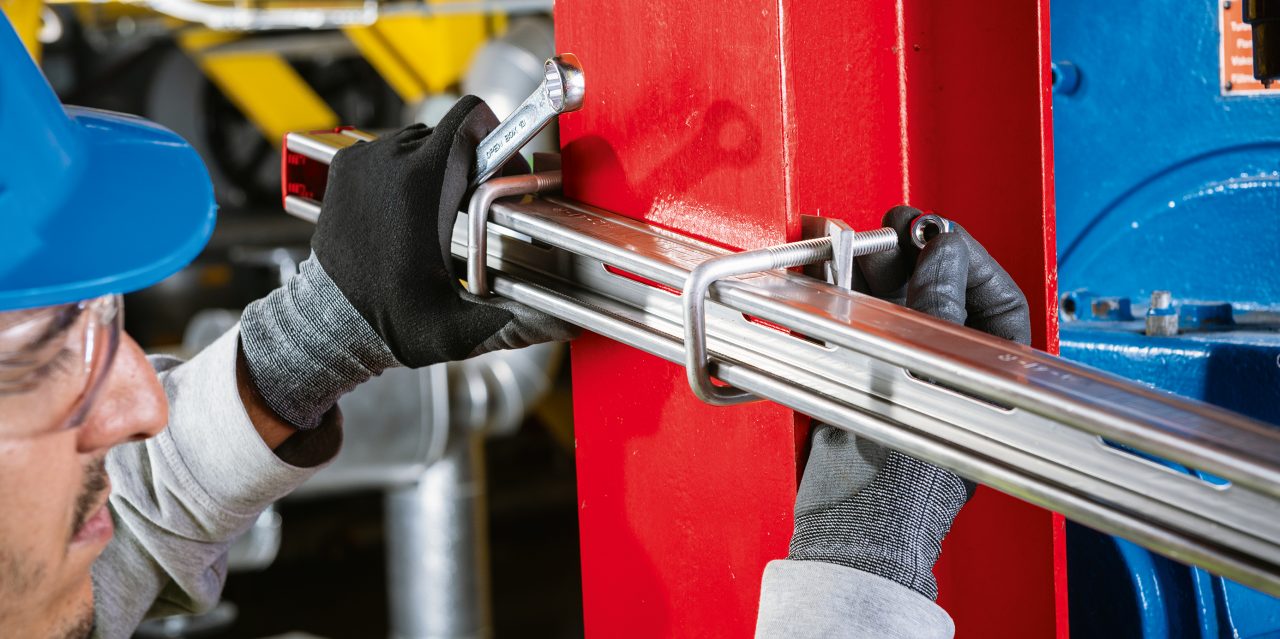
Traditional Method ─ Clamping
- Access from 2 sides needed
- Limits regarding fastening directions ─ allows horizontal fastening only
- Limited vibration resistance ─ more maintenance required
- Clamping scratches surface ─ rework of coated steel required
Innovative Hilti methods for fastening to steel
Hilti offers a variety of methods customized to various corrosive environments that help reduce or eliminate the drawbacks of traditional methods. Depending on the corrosive environment and type and thickness of the base material, Hilti offers three different fastening options. These solutions help maintain the corrosion resistance of the structural steel and the connection to the non-structural components.
Three fast and reliable ways for fastening to steel
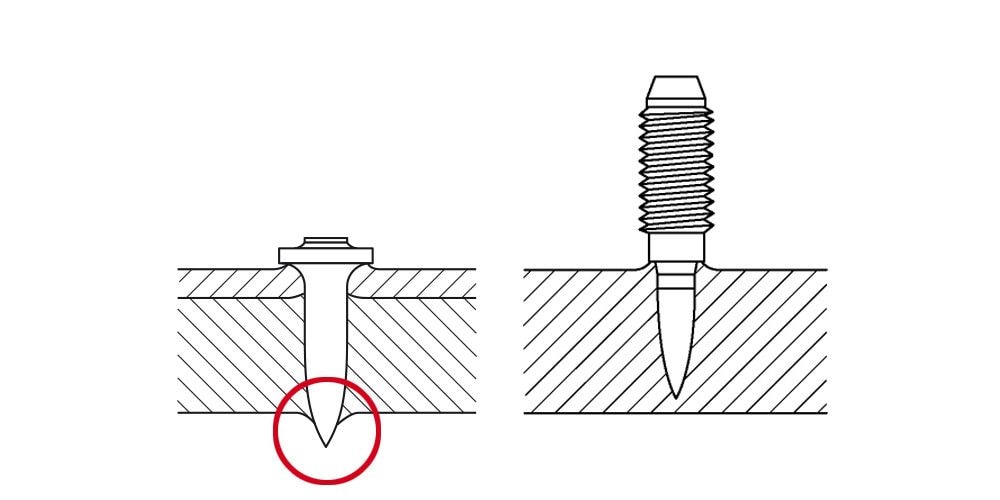
Sharp tip fastening
A fastening technology where a sharp tip stainless steel fastener is driven by a powder-actuated tool into the base material, creating a high-quality connection.
- Suitable for high-frequency fastening where the fastening can be completed in a few seconds
Stainless steel fasteners for mildly-corrosive environments where penetration through base steel is acceptable.
Watch the sharp tip video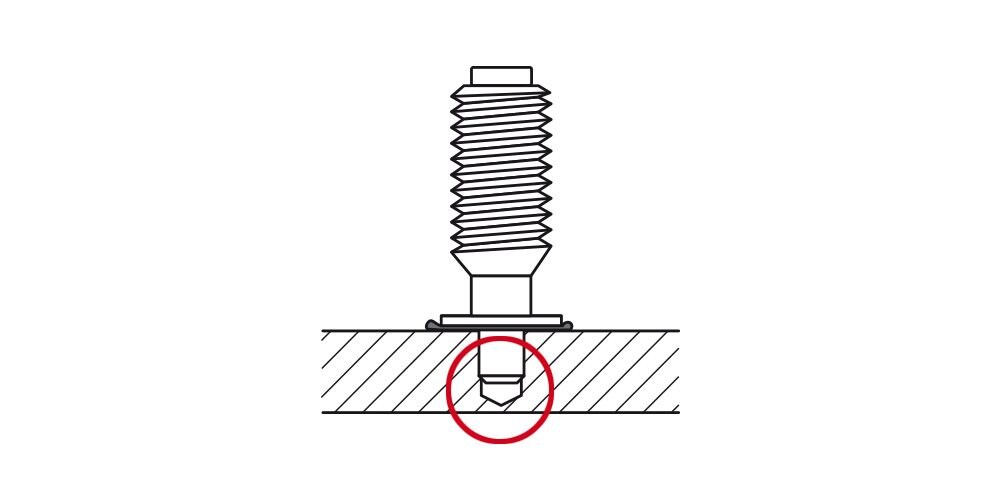
X-BT blunt tip fastening
A revolutionary fastening technology where a blunt-tip stainless steel fastener with a smooth cylindrical or conical shank is driven by a powder-actuated tool into a pre-drilled hole in the base material, creating a high-quality connection.
- No damage to the corrosion protection coating in non-through penetration applications
- Fastenings in less than 2 minutes
Duplex stainless steel fasteners for highly-corrosive environments. Fiber reinforced polymer (FRP) / duplex stainless steel fasteners for mildly-corrosive environments.
Watch the blunt tip video Download X-BT technical document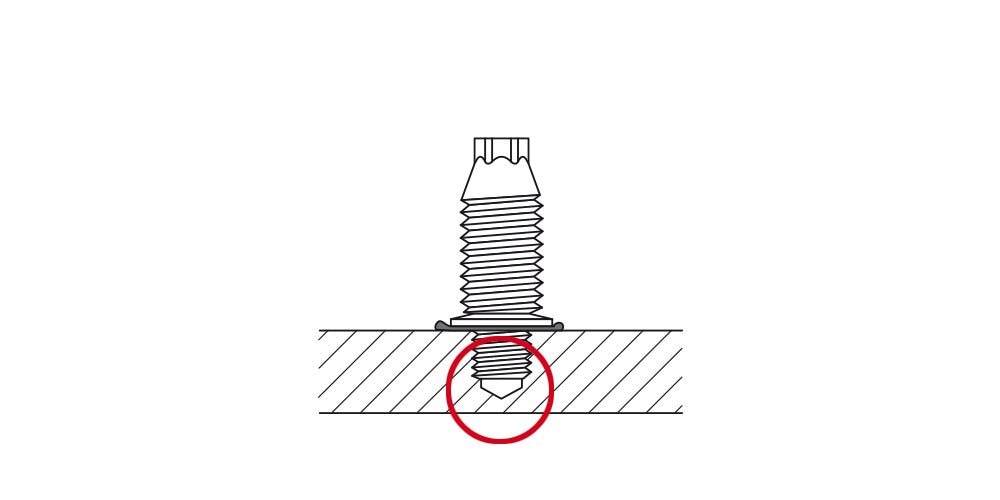
S-BT blunt tip screw fastening
A revolutionary fastening technology where a blunt-tip stainless steel fastener with a screw type shank is driven by a torque controlled screw driver into the pre-drilled hole in the base material creating a tapped connection.
- No damage to the corrosion protection coating in non-through penetration applications
- Fastenings in less than 2 minutes
Duplex stainless steel fasteners for highly-corrosive environments. Duplex coated carbon steel fasteners for mildly-corrosive environments.
Watch the blunt tip screw video Download S-BT technical documentWhich technology is right for me?
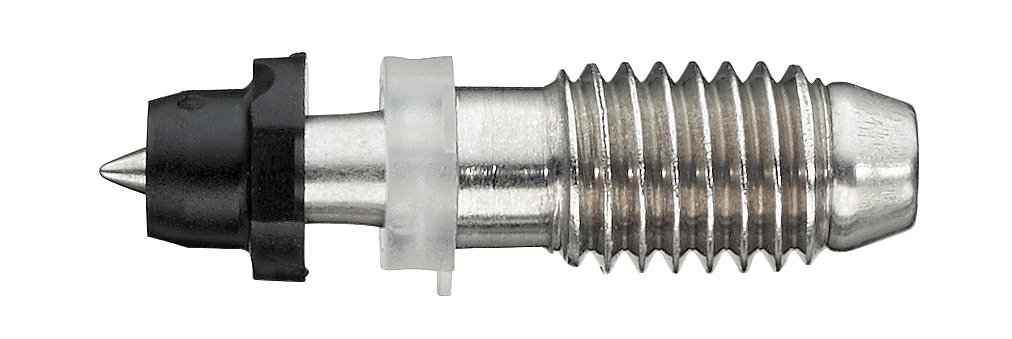
Sharp tip fastening
Base material
Steel
Minimum thickness
6 mm
Through penetration
Yes
Tool required
DX 5 or DX 450 or DX 460
Available thread diameter
M8
Fastener material
SS A2 equivalent
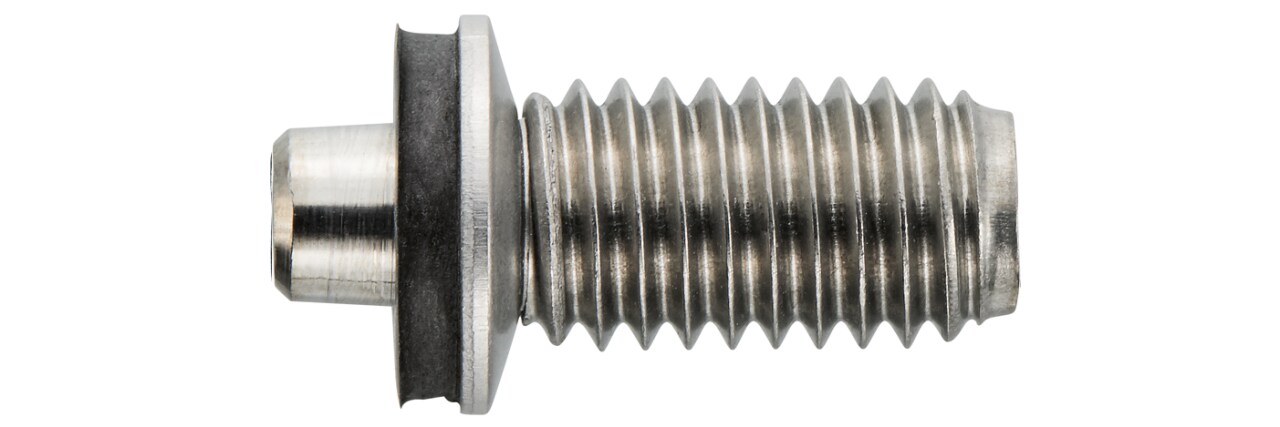
X-BT blunt tip fastening
Base material
Steel, stainless steel, cast iron
Minimum thichness
8 mm
Through penetration
No
Tool required
SF BT A22 and DX 351-BT(G)
Available thread diameter
M6, W6, M8, M10, W10
Fastener material
SS A4 equivalent and FRP (X-BT-MF)
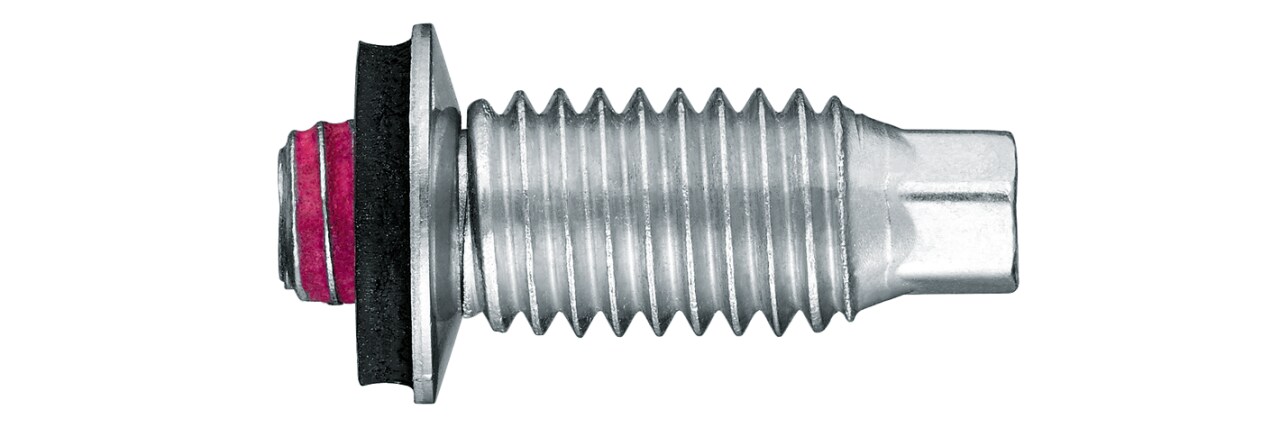
S-BT blunt tip screw fastening
Base material
Steel, aluminum
Minimum thichness
6 mm
Minimum thichness
No
Tool required
SBT 4-A22
Available thread diameter
M8, M10, W10
Fastener material
SS A4 equivalent and duplex coated carbon steel
Common Application of Direct Fastening ─ Solutions for your needs
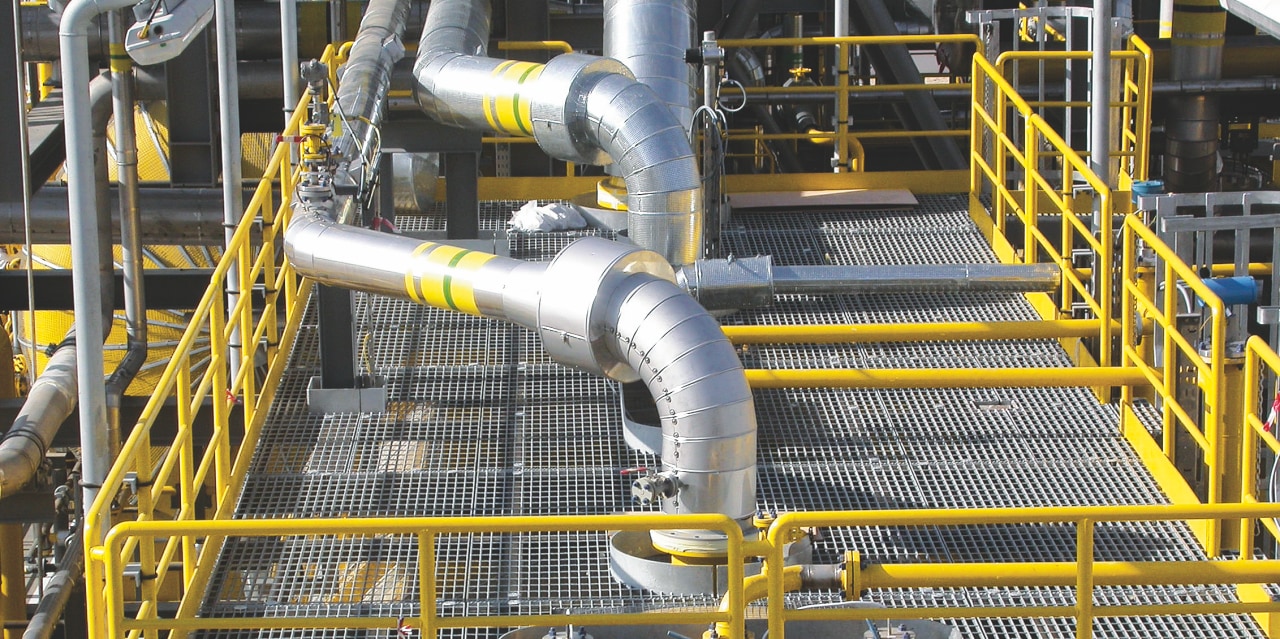
Grating & Industrial Flooring
Fastening gratings and industrial flooring to steel structures in the Oil & Gas as well as in the Power and Industry segments
- Efficient solutions for highly and mildly corrosive environments
- Internationally approved system solutions
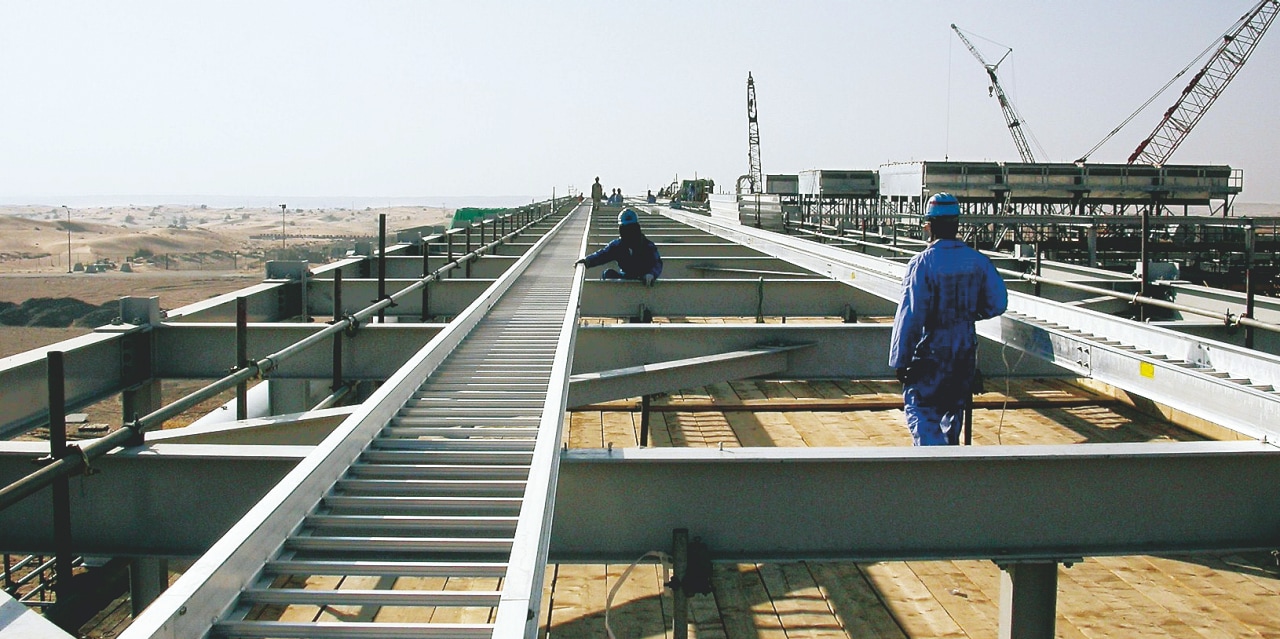
Multi Purpose Fastening Electrical
- Fastening of cable trays, cable ladders and electrical & instrumentation applications
- Efficient solutions for highly and mildly corrosive environments
- Internationally approved systems for all Energy & Industry segments
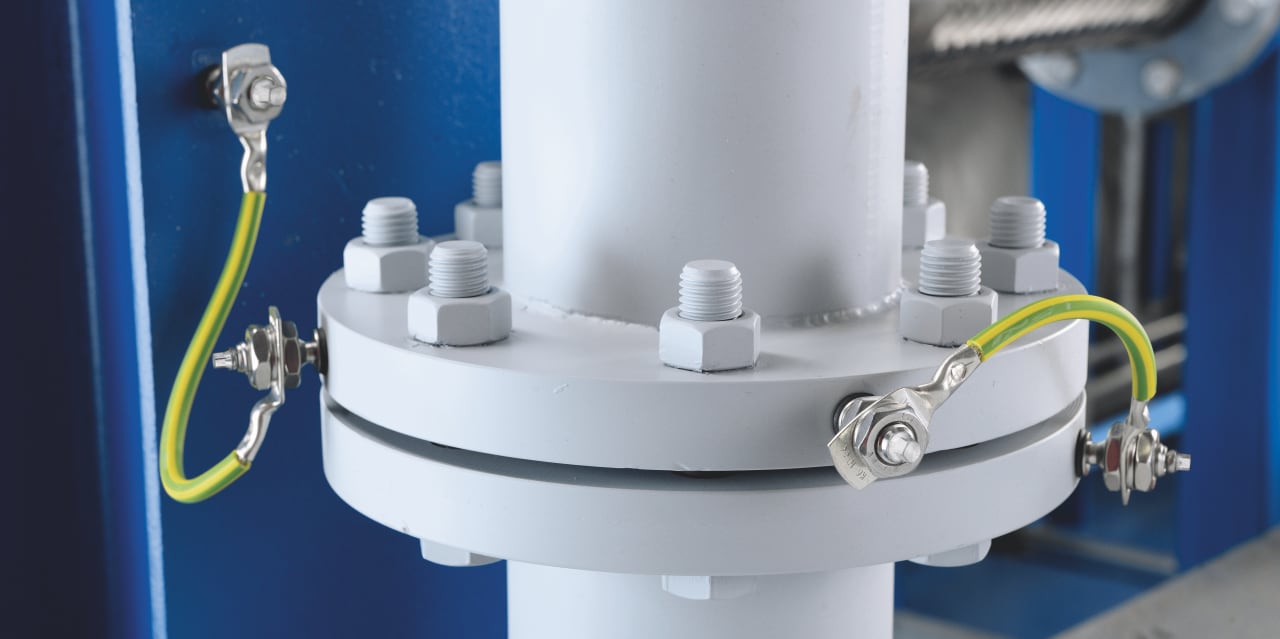
Electrical Connections
Setting up an electrical bonding and grounding connection to a steel base is an efficient solution for highly and mildly corrosive environments
- Increased speed & convenience
- No rework of steel coating required
- Internationally approved systems